Deprag Feeder Technology
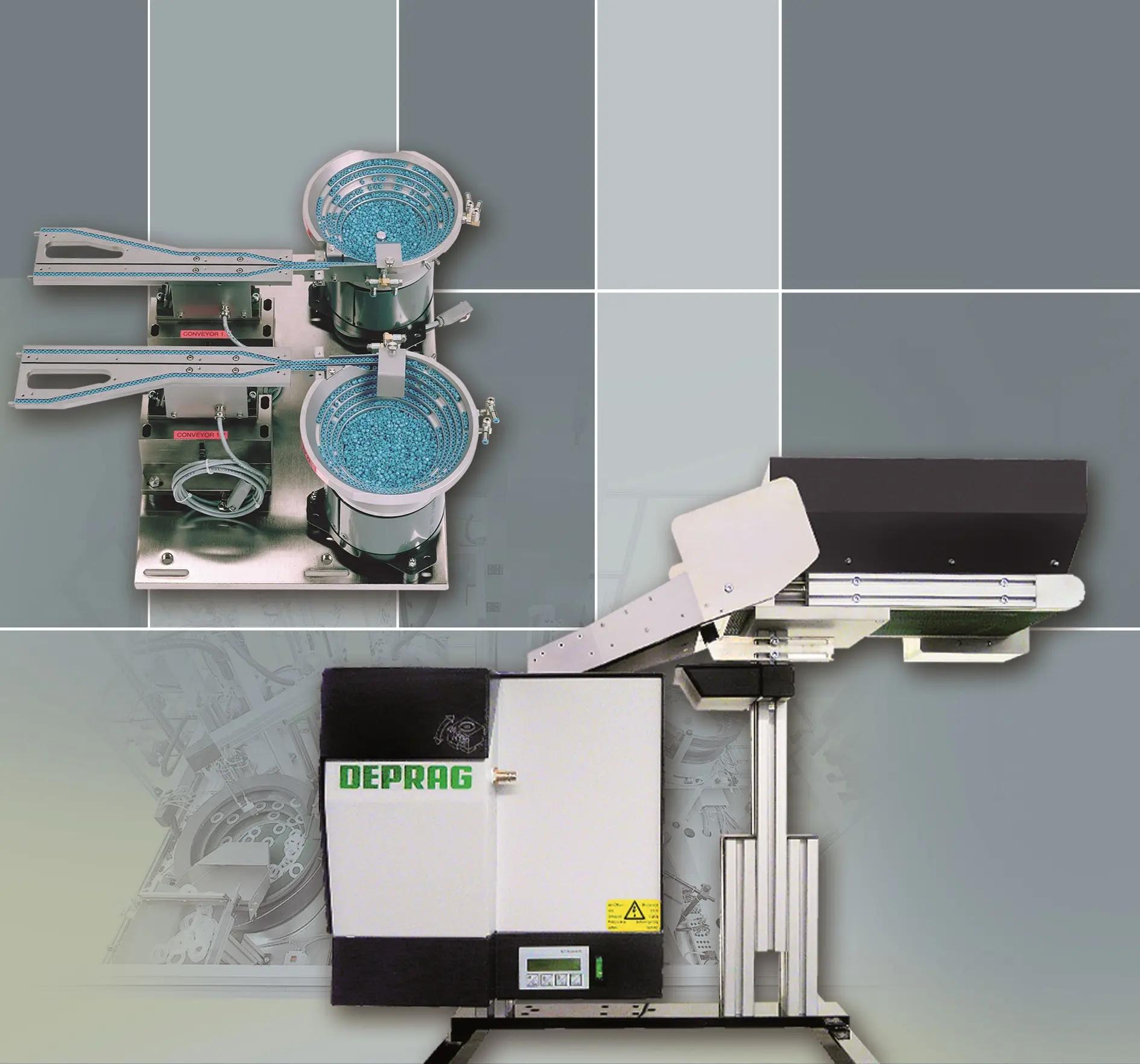
The obvious answer is that high powered grinders will save you money.
Apart from this, abrasive manufacturers are coming up with more aggressive disks for faster material removal. The problem with these new disks is that they will destroy most electric grinders and stall most air grinders because they need a high powered tool to run them. Some examples are the PFERD ALU-Master, CC-Grind disks and the Maija Frästechnik milling discs. These unique new products offer extremely fast material removal but require high powered grinders.
The PFERD ALUMASTER high speed discs are a unique tool that offers very fast material removal. It is ideal for use on aluminium because it does not produce hazardous or explosive dust.
It uses ten replaceable tungsten inserts to machine the aluminium rather than grind it. This also means that the tool doesn’t clog up.
These discs suit 115mm or 125mm grinders with a max speed of 13,300rpm and PFERD recommend an air grinder of at least 1000watts or an electric grinder of at least 1400watts
Another new disc that requires a high powered grinder are the Maija Frästechnik milling discs. These are available for a range of materials including steel, aluminium and titanium. Maija Frästechnik tested and recommend Deprag Turbine powered grinders for use with their discs.
Flow Drill Screws, Flow Form Screws
FDS® screws from EJOT and FFS® screws from Arnold have been around for a while. They offer the benefits of a secure and strong joint from one side between two sheet metals. A big advantage is that they can join dissimilar materials like aluminium, steel and plastics where spot welding is not possible (they are finding more and more applications in the automotive industry where aluminium and other materials need to be joined). They also allow the use of thinner sheets without the use of additional hardware to strengthen the joints (this is making them more popular in the whitegoods industries).
The screws form a hole by high pressure and the speed of the screw, the heated material is then threaded and cools around the screw. The joint is strong, and the unscrewing torque is high. The thread formed is upto 3 times thicker than the sheet metal.
Advantages for joining sheet metal: