Adaptive Sheet Metal Screwdriving Unit
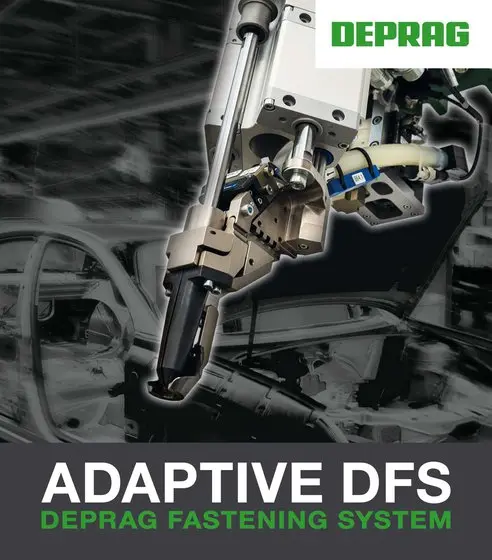
Flow Drill Screws, Flow Form Screws
FDS® screws from EJOT and FFS® screws from Arnold have been around for a while. They offer the benefits of a secure and strong joint from one side between two sheet metals. A big advantage is that they can join dissimilar materials like aluminium, steel and plastics where spot welding is not possible (they are finding more and more applications in the automotive industry where aluminium and other materials need to be joined). They also allow the use of thinner sheets without the use of additional hardware to strengthen the joints (this is making them more popular in the whitegoods industries).
The screws form a hole by high pressure and the speed of the screw, the heated material is then threaded and cools around the screw. The joint is strong, and the unscrewing torque is high. The thread formed is upto 3 times thicker than the sheet metal.
Advantages for joining sheet metal: